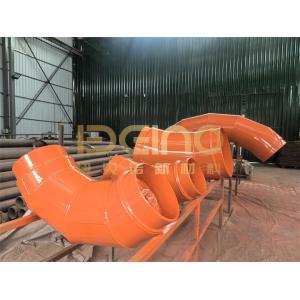
Add to Cart
Product Description
Large-diameter ceramic patch pipes are efficient transportation solutions designed specifically for industry. The core is to closely adhere high-purity alumina ceramic patches to the inner wall of the steel pipe to form a composite protective layer that is wear-resistant, high-temperature-resistant, and corrosion-resistant. The hardness of ceramic patches far exceeds that of ordinary steel, and can effectively cope with complex environments such as mining slurry erosion, high-temperature dust in power plants, and iron slag erosion in steel plants, making the service life of the pipeline more than 10 times that of ordinary steel pipes, significantly reducing the frequency of replacement and maintenance and downtime losses.
Our company produces ceramic pipes that support customization of pipe diameters from 300mm to 2400mm, which are used in transportation systems of different sizes. With professional installation guidance, we provide stable, reliable, and cost-optimized material transportation solutions for industries such as mining, power generation, and metallurgy.
Product Features
Application
Industry | Typical Applications | Pain Points Solved |
Mining | Slurry transportation for copper/gold ores, tailings pipelines | Frequent replacement due to severe abrasion |
Thermal Power | Flue gas desulfurization (FGD) systems, fly ash handling lines | Corrosion from acids/alkalis & high-temperature oxidation |
Steelmaking | Blast furnace coal injection pipes, sintered ore conveyors | Impact wear from metal particles |
Cement Production | Raw meal/clinker pneumatic conveying, kiln exhaust ducts | Erosion by high-temperature dust |
Ceramic technical parameters
Items | Specifications | |
Content of alumina | ≥92% | ≥95% |
Density | ≥3.6 g/cm3 | >3.8g/cm3 |
Rockwell A hardness | ≥82HRA | ≥85HRA |
Impact strength | ≥1200 MPA | ≥1500 MPA |
Fracture toughness | ≥3.8MPa·m1/2 | ≥4.0MPa·m1/2 |
Vickers hardness | ≥1150HV10 | ≥1200HV10 |
Bending Strength | ≥290MPa | ≥330MPa |
Product advantages
Life and cost comparison: The service life is more than 10 times that of ordinary steel pipes, and the maintenance frequency is reduced by 80%. The project cost is 20-30% lower than that of wear-resistant steel pipes, and the long-term operation cost is reduced by 45%.
Technological innovation: High temperature bonding technology: The adhesive has a temperature resistance of ≥350℃, ensuring that the ceramic sheet does not fall off in extreme environments.
Environmental protection and energy saving: The smooth inner wall design reduces the conveying resistance and saves more than 15% of energy consumption. Non-toxic and harmless, in line with international environmental protection standards.
Why choose us?
Strict quality assurance system
From product design and manufacturing to installation, it is fully incorporated into the ISO quality management system, each process is strictly implemented by the company's procedures and specifications, and strict quality control ensures that each product meets customer requirements. Each product must pass quality inspection before leaving the factory. All new products undergo rigorous wear simulation experiments
Perfect Service:
Our company has a professional technical research and development team and has accumulated more than ten years of experience in equipment anti-wear. According to the on-site information provided by customers, from material selection, and design to project budget, we analyze the causes of wear and tear, tailor-made anti-wear solutions, and provide design drawings.
well-experienced
Focusing on equipment anti-wear, we focus on communication with customers and experience accumulation. Many of our new products are inspired by customers. Iberno has been focusing on equipment anti-wear for more than ten years. The professional team is engaged in the research and development of new materials, friction and wear research, and engineering design. Has extensive experience.
FAQ
Q1: What is the maximum diameter of ceramic patch pipes that can be produced?
A1: Currently, we support customized pipes with diameters of DN30~DN2400 (or larger), which can be designed according to customer needs.
Q2: Will the ceramic patch fall off? How to ensure the bonding strength?
A2:The dual process of high-strength epoxy adhesive bonding + mechanical riveting is used to ensure that the ceramic patch does not fall off under impact and vibration. Passing ISO 9001 quality certification, each batch of pipes is tested for air tightness and impact.
Q3: Which industries and media are applicable?
A3: Industry: Mining tailings transportation, ash removal in thermal power plants, coal powder pipelines in cement plants, red mud transportation in aluminum plants, etc.
Medium: abrasive substances such as particles, slag, mortar, coal powder, etc. (temperature ≤ 150 ° C, special design is required for higher temperatures).
Q4: What should be noted during installation?
A4: Avoid direct welding and connect with flanges or clamps. Handle with care during lifting to prevent the ceramic layer from being impacted by external forces.
It is recommended to install flexible joints in the pipeline system to reduce the impact of vibration.
Q5: How long is the delivery cycle?
A5: Large diameter customized pipelines usually take 25~45 days (depending on the quantity and complexity of the process).